How is Iron Refined from Ore?
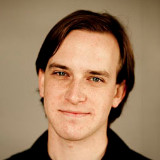
Iron ore is any rock that contains a usable quantity of iron. Common ore minerals include hematite, magnetite, limonite, and siderite, and these are frequently found together with assorted silicates. Although iron does not occur in its pure form in nature, some kinds of ore contain up to 70% iron atoms. Iron ore consists of oxygen and iron atoms bonded together into molecules. To create pure iron, one must deoxygenate the ore, leaving only iron atoms behind, which is the essence of the refining process.
To coax the oxygen atoms away from the ore requires heat and an alternate atomic partner for the oxygen to bond to. Carbon fills this role nicely, and is readily available in the form of everyday charcoal, or coke, a form of carbon made from coal. The carbon atoms bond with the oxygen in the ore to create carbon dioxide and carbon monoxide, gases that escape out a chimney. Because iron ore typically contains silicates, which do not bond to the carbon, these remain in the iron after it is refined, creating wrought iron, a malleable and strong form of metal used by blacksmiths throughout history.

To create an even purer form of iron, known as pig iron, limestone must be added to the mix and the heat increased. This is done contemporarily in the silo-like structure known as a blast furnace. The calcium in limestone bonds with the silicates in the ore, creating a material called slag, which floats on top of the pure liquid iron. The iron is periodically drained into a mold from a port at the bottom of the blast furnace, where it cools. The pig iron can then be converted into wrought iron by mixing it with silicon, or processed further to create steel.
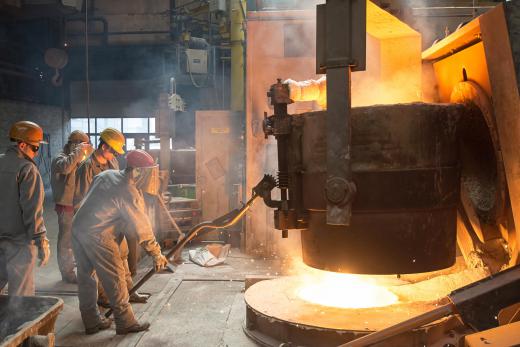
Steel is a form of iron mixed together with 0.5% - 1.5% carbon but no oxygen, silicates, or other impurities. This metal is much more difficult to work than wrought iron, but is greatly stronger. Iron can be mixed together with various other elements to create alloys with desired properties, such as lightness or resistance to rust (stainless steel).

Because iron is so common (composing 5% of the Earth's crust), strong, and relatively easy to process, it plays a very intimate role in human civilization. Roughly 98% of all ore shipped worldwide is used in the production of iron or steel. Surface deposits are abundantly available in most geographic areas. Ancient civilizations that reached the threshold level of technology required to smelt iron ore enjoyed decisive advantages over their competitors, whose bronze and copper weapons were no match for ironworks.
AS FEATURED ON:
AS FEATURED ON:


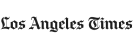

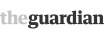
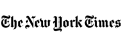
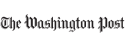


Discussion Comments
Extremely helpful. Thank you, wiseGeek!
This was a little helpful but like others, I need much more for my 18 page assignment, including what the properties of processed iron after it has been refined as well. Thanks anyway!
very helpful for my assignment. Thanks a lot.
This article was useful for my studies. It made me understand this lesson.
yeah some more info and hard facts would be nice but pretty good overall.
When there is silver, copper and gold in the iron ore does it stay in the iron or go into the slag?
It helped me a lot on my project and now I have a LOT of jot notes for my project.
Thank you! This helped me greatly with the Geology merit badge in Boy Scouts. I needed to explain how a resource that can be extracted from the Earth can be refined/processed, and this helped greatly. Not too hard to understand yet it provides enough material to be helpful. Thank you!
It was helpful but I needed more info on which refining process is used for iron, like smelting, electrolysis or displacement so I could use it for my school project.
I found this subject helpful for my school project but I need more information like what the properties of all the processed products of Iron Ore after it has been refined.
Post your comments