What Is a Force Gauge?
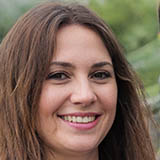
A force gauge measures the force applied to an object. It can be used in routine testing and maintenance in manufacturing and other settings, or for activities like finding the failure point of a material or testing laden equipment. Some force gauges are analog, while others work with a digital scale. One advantage of digital scales is the ability to record data during testing by hooking the equipment up to a base unit.
High levels of force can result in strain on the underlying material. This can cause it to warp or fail. In materials testing, it may be important to know when the strain overloads the integrity of the material, as this can determine whether it meets standards. On children’s toys, for example, the manufacturer may set a limit to ensure that regular play will not tear off extremities and dangling parts. If these parts broke off under low pressure, they might present a hazard to children at play.
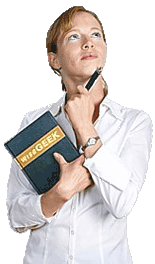
The inside of the force gauge includes a spring that expands and contracts. As it expands, it either feeds directly to a dial with a needle that measures force, or converts the strain into voltage and generates a digital readout. Very high quality metal alloys capable of handling intense strain are used in the construction of force gauge, allowing it to measure extremely high values. Durable, resistant materials are also used for the housing and other components to ensure the device itself doesn’t break during procedures.
This equipment is designed for push and pull testing, where force is slowly and steadily applied to components. A force gauge cannot be used in impact testing and similar activities, where force may be abrupt. The equipment is not designed to measure rapidly applied forces and can fail. It is also important to make sure that the equipment and components being tested are in alignment and secured before starting testing. Errors may result in inaccurate readings or damage.
Periodic calibration may be necessary to keep a force gauge in good working order. Over time, the springs and other components can stretch, and may no longer read with the necessary accuracy. A technician can test the equipment against other machines to determine if it reads correctly. If it does not, the spring may need to be replaced, or other adjustments to the inside of the machine may be necessary.
AS FEATURED ON:
AS FEATURED ON:


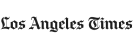

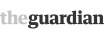
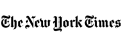
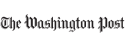


Discuss this Article
Post your comments