What is Durometer Hardness?
Durometer hardness is used to describe both the hardness of a material and the tool used to measure it. Typically used for rubber, plastics, and other polymers, durometer test results apply a specific value to the hardness of a material. Many people use these results to gauge the strength of a product, but that is not what this test was designed for. Rather than strength or durability, the durometer hardness scale measures the flexibility of the tested sample. This can be helpful when selecting the best material for a particular project.
The durometer hardness scale, which was developed by Albert Shore in the 1920s, refers to a material's resistance to permanent indentation when a specific amount of pressure is applied. A deeper indentation indicates a softer material, and a lower durometer number. The softest material would have a durometer value of zero, but the scale goes as high as 100 for the hardest plastics. Using a numeric scale like this makes it easy to determine the difference between various products, even when one does not know what the specific numbers mean.
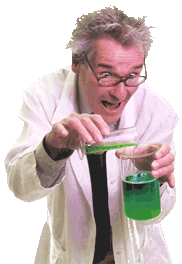
A total of 12 Shore durometer hardness scales have been developed over the years, but only two are widely used today. The Shore A chart, normally used for softer plastics, and the Shore D chart, which is reserved for more rigid materials. According to the American Society for Testing and Materials (ASTM), both scales use the same 0-100 scale, but rely on somewhat different durometer hardness testing tools and methods.
The actual test apparatus is called a durometer, or durometer hardness tester. They are available in many styles, but they all use the same basic mechanism to achieve the test result. The mechanism in question is a hardened steel rod attached to a gauge.
The difference between the durometer testers for Shore charts A and D can be found right at the tip of the steel rod. The rod for the chart A durometer tapers to a point, at a 35° angle. The chart D tester is tapered at a 30° angle and is slightly larger in diameter.
Durometer hardness testing standards in North America are determined by ASTM test method DD2240 00, and around the world by ISO 7619 and ISO 868. Under these standards, the method for Shore chart A testing is to apply the rod, also called the indenter, to the material with a predetermined amount of force for 15 seconds. The depth of penetration determines the durometer number. If there is no penetration, that material would be said to have a durometer of 100. An indentation of .09 inches (2.5 mm), on the other hand, would show a durometer of 0.
The type D tester is used the same way. The biggest difference, aside from the size and shape of the indenter, is that durometer hardness testing for chart D requires more than 5 times as much force as the same test for chart A. That's why this is the preferred method for harder materials.
AS FEATURED ON:
AS FEATURED ON:


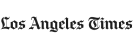

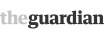
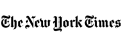
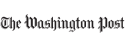


Discuss this Article
Post your comments