What Is Fractional Distillation?
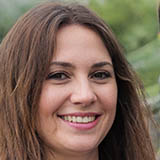
Fractional distillation separates mixtures into component products in a single distillation column. It involves heating a mixture to vaporize it, and forcing it through the column, where various products will condense and precipitate out in response to temperature changes. This technique is widely used in industrial chemistry for the processing of products like crude oil and air. The method can also be applied in experimental settings to distill samples of interest.
The process of fractional distillation can be used in any setting where a mixture includes a blend of components with similar, but not identical, vapor points. Conventional distillation may not be adequate to the needs of such mixtures, or could require multiple passes to extract the desired components. With mixtures of unknown makeup, a chemist can perform some simple tests on a sample to determine what it contains and decide how to separate it. The best option can depend on how the sample will be used.
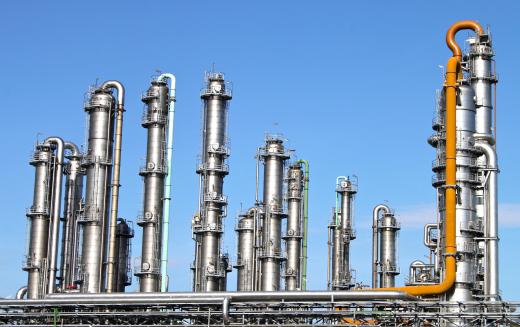
Equipment heats the mixture during fractional distillation, causing it to boil and throw off vapor. The vapor rises through a column lined with trays. As it cools, it condenses, and each tray captures a different condensate. Materials that condense at relatively high temperatures drop out first. As the mixture grows steadily cooler, other compounds condense, until it hits the top of the column. The system can drain each tray separately to capture the distillates. This allows for recovery of all useful components in the mixture.
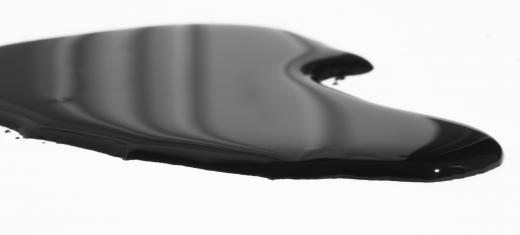
The type of required equipment can vary in size and composition, depending on what kinds of materials are being processed. Facilities like oil refineries need to recover as much as possible from each barrel of oil, and have extensive distillation facilities capable of handling very high volumes of material. In a lab setting, the equipment may be relatively small, as the samples are usually not very large. A desktop fractional distillation unit may be an option for some lab settings.
Students in chemistry classes may learn about fractional distillation and have an opportunity to practice it in a lab setting. The technology is used in a wide variety of industries, and chemists may go on to specialize in distillation techniques used with particular materials. Petroleum chemists, for example, study this process as well as techniques like cracking to break up hydrocarbon chains in crude oil. Cracking can be used to change the chemical composition of oil to extract more useful components.
AS FEATURED ON:
AS FEATURED ON:


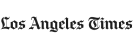

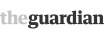
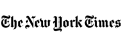
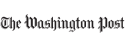


Discussion Comments
@submariner- Creating liquid coal fuels is still in the developmental stage and is not yet commercially scalable. Currently the best use for coal is the production of synthetic gas (syngas) for electricity generation.
A syngas plant is also known as a Integrated Gasification Combined Cycle (IGCC) power plant. These plants work by heating the coal to a critical point, causing the hydrocarbons to vaporize. The gas is then passed over a bed of coals which filter out mercury and other heavy metals. The gas is then processed to remove and alter sulfur and nitrogen content. These are the pollutants that cause smog and acid rain, so essentially the syngas is cleaned.
Once cleaned, the gas is burned to run a turbine and generate electricity. After this first combustion cycle, the heat is recovered and used to heat steam to turn another turbine, significantly improving efficiency. The process is similar to oil fractional distillation, but not the same. As of now, this is currently the cleanest coal combustion technique. Plant efficiencies can reach 50% and emissions can be reduced by about 20%, but it is still a long way off from zero emissions.
@submariner- The fractional distillation of crude oil produces a number of products that are used for everything from fuel to chemical production to road building. When petroleum is refined, the boiler breaks the long chain hydrocarbons in crude oil, and other pollutants like sulphur and heavy metals are processed out. The process results in heavier long chain hydrocarbons accumulating at the bottom of the tower, and lighter short chain hydrocarbons raising to the top.
The lightest hydrocarbons are gases such as methane, ethane, propane and butane float to the top. These products are used as auto fuels, cooking fuels, electricity generation, and plastic production. The next lightest hydrocarbons are napthas and ligroins that will be rerouted to the reformer to form longer chain hydrocarbons like gasoline. The third highest layer are the gasoline hydrocarbons having 5 to 12 carbon atoms per molecule.
The next lowest layer are kerosene and diesel, used as heating oil, jet fuel, and fuel for tractors and trucks. Even lower are the lubricating oils and heavy fuel oils. These are used to make automotive lubricants, grease, and fuel for industrial turbines. These can also be rerouted for further cracking to make lighter products. Finally, you have the residuals that are used to make concrete, asphalt and waxes.
What are the different products created in the fractional distillation process? I am specifically interested in the products created in crude oil production.
Also, How is coal turned into liquid fuels and how do these fuels compare to gasoline and diesel? Do coal fuels create cleaner or dirtier emissions than hydrocarbon fuels? I am trying to write a paper on fuel energy production and I want to know if the costs of converting coal to liquid fuels is justified by the added energy security of having multiple sources of fuel.
Post your comments