What is Process Plant Design?
Process plant design involves the planning of various processes needed to accomplish a physical or chemical transformation of certain types of materials. Process plant design may be used to design a new facility or to expand or modify an existing facility. Although it typically begins at a conceptual level, process plant design usually ends with the creation of some type of fabrication or construction plans. The designers of a chemical process facility usually write various types of operating manuals detailing procedures required to start-up, operate, and shut-down the facility. These documents may also be needed for future modifications to the facility.
Before beginning a complex project, process plant designers typically gather data from small pilot plants as well as other larger facilities currently in operation. Process plant design also requires extensive data gathered from a variety of other sources such as testing laboratories and equipment manufacturers. The design of a process plant facility must not only accomplish the desired production objectives; it must also stay within the boundaries of certain other constraints as well. These constraints typically include such things as space availability, environmental impact, and safety issues, as well as capital, operating and maintenance costs.
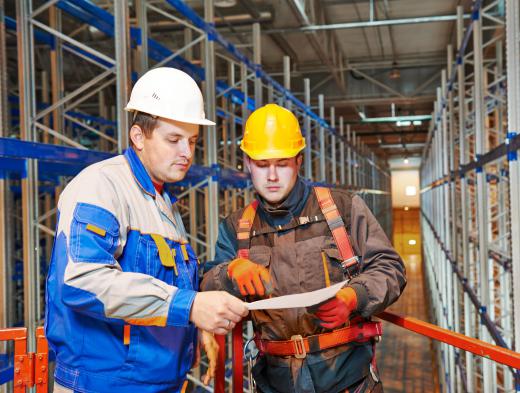
Prior to submitting a proposal for a new process facility, researchers will often test the process on a very small scale first. Results from these small tests are then used to determine the feasibility of the process on a much larger scale. A small pilot plant is usually constructed for this purpose. After gathering the necessary data from the pilot plant, researchers usually form a process plant design team composed of scientists and engineers in order to draw up the construction plans for the new facility. This team must also write a variety of different operating manuals as well.
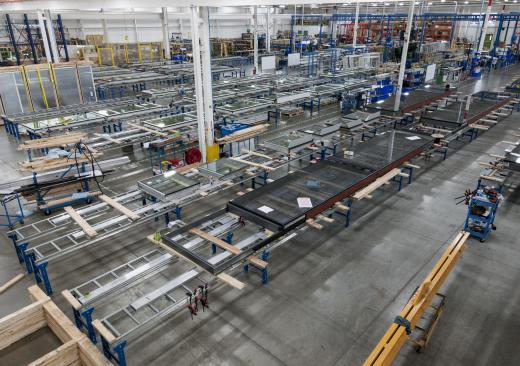
A wide variety of factors must be considered in the design of a typical process plant facility. The dimensions, lengths, and operating parameters of various pumps and pipes must be determined as well as the availability of water and electricity. Additional pumps and piping needed for plant start-up and shutdown procedures must be included in the design as well. Planners must also design methods for taking product samples when necessary. After the entire processing facility has been designed, engineers will typically use computer simulations to analyze parameters such as rate of flow, working pressures, and temperatures in an effort to ensure that the entire process will perform safely and efficiently.
AS FEATURED ON:
AS FEATURED ON:


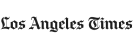

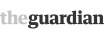
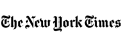
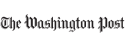


Discussion Comments
@Charred - I’m not opposed to industrial plant design, but I think more attention should be paid to building eco friendly plants.
I realize that under current laws they take into account environmental impacts, but they should do more than make sure their designs satisfy current regulations. Instead, they should actively pursue new designs that will have a positive environmental impact.
That way, years down the road they will avoid any potential scuffles with the EPA. After all, regulations do change, and it’s possible that future regulations will be stricter than those that are currently on the books.
I like the idea of building a prototype process plant on a small scale before building the full scale model. I can think of at least one positive benefit to this approach, besides improved processes.
I think you would be able to detect possible safety hazards; perhaps there would be a chemical leak somewhere or excess pollution that you had not factored into your calculations for the large scale plant design.
If that is the case, at least you can contain it by working with the prototype, and then making corrections before you build the full scale facility.
Post your comments